Calibração de transmissores: Exatidão em Medições
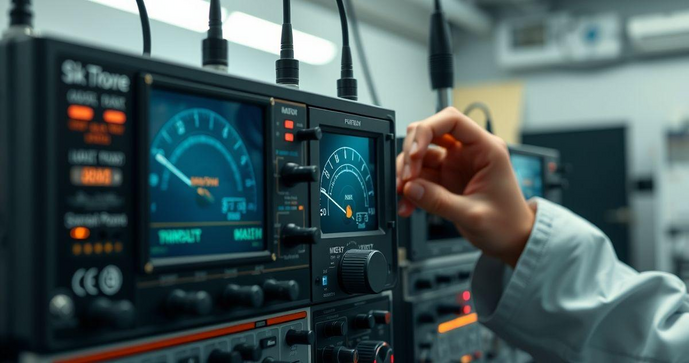
Por: Redator - 01 de Julho de 2025
A calibração de transmissores é um processo fundamental para garantir a precisão e a confiabilidade dos dados coletados em diversas aplicações industriais e laboratoriais. Com o avanço da tecnologia, a necessidade de manter os equipamentos calibrados se torna cada vez mais crítica, pois pequenas variações podem impactar significativamente os resultados. Neste artigo, abordaremos a importância da calibração, o passo a passo para realizá-la corretamente, os erros comuns a serem evitados e a importância da manutenção regular dos transmissores calibrados.
Importância da Calibração de Transmissores para a Precisão dos Dados
A calibração de transmissores é um procedimento essencial em diversos setores, incluindo indústrias químicas, petroquímicas, farmacêuticas e de alimentos. Esses dispositivos são responsáveis por medir e transmitir dados críticos, como pressão, temperatura, nível e vazão. A precisão desses dados é vital para garantir a segurança, a eficiência e a qualidade dos processos industriais. Quando os transmissores não estão calibrados corretamente, os dados que eles fornecem podem ser imprecisos, levando a decisões erradas e, consequentemente, a problemas significativos.
Um dos principais motivos pelos quais a calibração é tão importante é a necessidade de conformidade com normas e regulamentos. Muitas indústrias operam sob rigorosos padrões de qualidade e segurança, que exigem que os equipamentos de medição sejam calibrados regularmente. A falta de calibração pode resultar em não conformidade, o que pode levar a penalidades, multas e até mesmo à interrupção das operações. Além disso, a calibração adequada é frequentemente um requisito para a obtenção de um certificado de calibração rbc, que é um documento que atesta a precisão e a confiabilidade dos instrumentos de medição.
Outro aspecto importante da calibração de transmissores é a prevenção de falhas nos processos. Transmissores imprecisos podem levar a leituras erradas, que, por sua vez, podem resultar em falhas operacionais. Por exemplo, em uma planta de processamento químico, um transmissor de pressão que não está calibrado corretamente pode indicar uma pressão mais baixa do que a real, levando a uma operação insegura e potencialmente catastrófica. A calibração regular ajuda a garantir que os transmissores funcionem dentro das especificações, minimizando o risco de falhas e melhorando a segurança geral do ambiente de trabalho.
Além disso, a calibração de transmissores contribui para a eficiência operacional. Quando os dados fornecidos pelos transmissores são precisos, as decisões tomadas com base nesses dados são mais confiáveis. Isso pode resultar em uma melhor alocação de recursos, otimização de processos e redução de desperdícios. Por exemplo, em um sistema de controle de temperatura, um transmissor calibrado corretamente pode ajudar a manter a temperatura ideal, evitando o superaquecimento ou o resfriamento excessivo, o que pode resultar em perda de produto e aumento de custos.
A calibração também desempenha um papel crucial na manutenção da qualidade do produto. Em indústrias alimentícias e farmacêuticas, a precisão das medições é fundamental para garantir que os produtos atendam aos padrões de qualidade. Um transmissor que não está calibrado pode levar a variações na composição do produto, resultando em produtos fora das especificações e, potencialmente, em recalls. A calibração regular ajuda a garantir que os produtos finais sejam consistentes e de alta qualidade, protegendo a reputação da empresa e a segurança do consumidor.
Além disso, a calibração de transmissores é uma prática que pode ajudar a prolongar a vida útil dos equipamentos. Quando os transmissores são calibrados regularmente, é possível identificar problemas antes que se tornem sérios. Isso permite que as empresas realizem manutenções preventivas, evitando falhas inesperadas e custos de reparo elevados. A manutenção regular, aliada à calibração, pode resultar em uma operação mais suave e eficiente, reduzindo o tempo de inatividade e aumentando a produtividade.
Por fim, a calibração de transmissores é uma prática que promove a confiança nas medições. Em um ambiente industrial, onde decisões críticas são tomadas com base em dados, a confiança na precisão das medições é fundamental. A calibração regular ajuda a construir essa confiança, garantindo que os dados sejam consistentes e confiáveis ao longo do tempo. Isso não apenas melhora a eficiência operacional, mas também fortalece a reputação da empresa no mercado.
Em resumo, a calibração de transmissores é um aspecto vital para garantir a precisão dos dados em ambientes industriais. Ela não apenas assegura a conformidade com normas e regulamentos, mas também previne falhas operacionais, melhora a eficiência, mantém a qualidade do produto e prolonga a vida útil dos equipamentos. Portanto, investir em um programa de calibração regular é uma decisão inteligente que pode trazer benefícios significativos para qualquer organização.
Passo a Passo para Realizar a Calibração de Transmissores
A calibração de transmissores é um processo crítico que garante a precisão e a confiabilidade dos dados coletados em diversas aplicações industriais. Realizar a calibração de forma adequada requer um conjunto de etapas bem definidas. A seguir, apresentamos um guia passo a passo para realizar a calibração de transmissores, assegurando que você obtenha resultados precisos e confiáveis.
1. Preparação e Planejamento
Antes de iniciar o processo de calibração, é fundamental realizar um planejamento adequado. Isso inclui a definição do tipo de transmissor a ser calibrado, a coleta de informações sobre as especificações do fabricante e a verificação dos equipamentos necessários para a calibração. Além disso, é importante garantir que você tenha acesso a um ambiente controlado, onde as condições de temperatura e pressão sejam estáveis, pois isso pode afetar os resultados da calibração.
2. Reunir os Equipamentos Necessários
Para realizar a calibração, você precisará de alguns equipamentos essenciais, como:
- Um calibrador de pressão ou temperatura, dependendo do tipo de transmissor que está sendo calibrado.
- Um multímetro, se o transmissor for elétrico.
- Conectores e mangueiras apropriadas para a conexão entre o transmissor e o calibrador.
- Documentação do fabricante, que pode incluir gráficos de calibração e especificações técnicas.
Certifique-se de que todos os equipamentos estejam em boas condições de funcionamento e calibrados, pois isso garantirá a precisão dos resultados.
3. Desconectar o Transmissor
Antes de iniciar a calibração, é necessário desconectar o transmissor do sistema em que está instalado. Isso pode envolver a despressurização do sistema e a remoção de conexões elétricas. É importante seguir as diretrizes de segurança ao realizar essa etapa, garantindo que não haja riscos de vazamentos ou acidentes.
4. Conectar o Transmissor ao Calibrador
Após desconectar o transmissor, conecte-o ao calibrador de pressão ou temperatura. Certifique-se de que as conexões estejam firmes e seguras para evitar vazamentos. Se o transmissor for elétrico, conecte os fios de acordo com as instruções do fabricante. Verifique se o calibrador está configurado corretamente para o tipo de medição que você está realizando.
5. Realizar a Calibração
Com o transmissor conectado ao calibrador, inicie o processo de calibração. Isso geralmente envolve a aplicação de uma série de pressões ou temperaturas conhecidas ao transmissor e a comparação das leituras do transmissor com as do calibrador. Registre as leituras em diferentes pontos de calibração, que devem abranger toda a faixa de operação do transmissor.
Durante este processo, é importante ajustar o transmissor conforme necessário. Isso pode incluir a utilização de botões de ajuste ou software de configuração, dependendo do modelo do transmissor. Siga as instruções do fabricante para garantir que os ajustes sejam feitos corretamente.
6. Documentar os Resultados
Após concluir a calibração, documente todos os resultados obtidos. Isso deve incluir as leituras do transmissor e do calibrador em cada ponto de calibração, bem como quaisquer ajustes realizados. A documentação é essencial para garantir a rastreabilidade e a conformidade com as normas de qualidade. Além disso, ela pode ser útil para futuras calibrações e manutenções.
7. Desconectar e Reinstalar o Transmissor
Depois de documentar os resultados, desconecte o transmissor do calibrador e reinstale-o no sistema. Certifique-se de que todas as conexões estejam firmes e seguras. Se necessário, realize a pressurização do sistema novamente, seguindo as diretrizes de segurança.
8. Testar o Sistema
Após a reinstalação do transmissor, é importante realizar um teste do sistema para garantir que tudo esteja funcionando corretamente. Verifique se as leituras do transmissor estão dentro das especificações e se o sistema responde adequadamente às mudanças nas condições de operação. Isso ajudará a identificar qualquer problema que possa ter surgido durante o processo de calibração.
9. Manutenção Regular
A calibração de transmissores não deve ser vista como uma tarefa única, mas sim como parte de um programa de manutenção regular. É recomendável estabelecer um cronograma de calibração baseado nas recomendações do fabricante e nas necessidades específicas da sua operação. A manutenção regular não apenas garante a precisão dos dados, mas também prolonga a vida útil dos equipamentos.
Realizar a calibração de transmissores é uma prática essencial para garantir a precisão e a confiabilidade dos dados em ambientes industriais. Ao seguir este passo a passo, você estará melhor preparado para realizar calibrações eficazes e contribuir para a eficiência e segurança da sua operação. Para mais informações sobre práticas e equipamentos de calibração, consulte especialistas em Instrumentação industrial e mantenha seus sistemas sempre em conformidade.
Erros Comuns na Calibração e Como Evitá-los
A calibração de transmissores é um processo crítico que garante a precisão e a confiabilidade dos dados em diversas aplicações industriais. No entanto, existem erros comuns que podem comprometer a eficácia desse procedimento. Identificar e evitar esses erros é fundamental para garantir que os transmissores funcionem corretamente e que os dados coletados sejam precisos. A seguir, discutiremos alguns dos erros mais frequentes na calibração e como evitá-los.
1. Falta de Planejamento Adequado
Um dos erros mais comuns na calibração de transmissores é a falta de planejamento. Muitas vezes, os profissionais iniciam o processo sem uma compreensão clara das especificações do transmissor ou dos requisitos de calibração. Isso pode levar a medições imprecisas e a ajustes inadequados. Para evitar esse erro, é essencial revisar a documentação do fabricante e estabelecer um plano de calibração que inclua todos os passos necessários, os equipamentos a serem utilizados e as condições ambientais ideais.
2. Uso de Equipamentos Não Calibrados
Outro erro frequente é o uso de equipamentos de calibração que não estão calibrados ou que não estão em boas condições de funcionamento. Isso pode resultar em medições imprecisas e comprometer todo o processo de calibração. Para evitar esse problema, sempre verifique se os equipamentos de calibração, como manômetros e multímetros, estão calibrados e em conformidade com as normas aplicáveis. Além disso, mantenha um registro da calibração dos equipamentos para garantir a rastreabilidade.
3. Ignorar as Condições Ambientais
As condições ambientais, como temperatura e pressão, podem afetar significativamente os resultados da calibração. Ignorar esses fatores pode levar a medições imprecisas. É importante realizar a calibração em um ambiente controlado, onde as condições sejam estáveis e dentro das especificações recomendadas pelo fabricante. Se não for possível calibrar em condições ideais, registre as condições ambientais durante o processo e considere isso ao interpretar os resultados.
4. Não Realizar Testes de Verificação
Após a calibração, é fundamental realizar testes de verificação para garantir que o transmissor esteja funcionando corretamente. Muitos profissionais cometem o erro de não realizar esses testes, o que pode resultar em problemas não detectados. Para evitar isso, sempre execute testes de verificação após a calibração, comparando as leituras do transmissor com um padrão conhecido. Isso ajudará a identificar qualquer discrepância e a garantir que o transmissor esteja operando dentro das especificações.
5. Ajustes Inadequados
Durante o processo de calibração, é comum que os profissionais façam ajustes no transmissor. No entanto, ajustes inadequados ou excessivos podem comprometer a precisão do dispositivo. Para evitar esse erro, siga as instruções do fabricante ao fazer ajustes e evite realizar alterações desnecessárias. Além disso, documente todos os ajustes realizados para referência futura.
6. Falta de Documentação
A documentação é uma parte crucial do processo de calibração. Muitos profissionais falham em registrar os resultados da calibração, os ajustes feitos e as condições em que a calibração foi realizada. Isso pode dificultar a rastreabilidade e a conformidade com as normas. Para evitar esse erro, mantenha registros detalhados de cada calibração, incluindo datas, resultados, ajustes e condições ambientais. Isso não apenas ajuda na conformidade, mas também facilita futuras calibrações e manutenções.
7. Não Treinar a Equipe Adequadamente
A calibração de transmissores requer conhecimento técnico e habilidades específicas. Um erro comum é não treinar adequadamente a equipe responsável pela calibração. Isso pode levar a procedimentos inadequados e a resultados imprecisos. Para evitar esse problema, invista em treinamento regular para a equipe, garantindo que todos estejam atualizados sobre as melhores práticas e os procedimentos corretos de calibração.
8. Ignorar a Manutenção Preventiva
A manutenção preventiva é essencial para garantir que os transmissores funcionem corretamente ao longo do tempo. Ignorar a manutenção pode levar a falhas e a necessidade de calibrações mais frequentes. Para evitar esse erro, estabeleça um programa de manutenção preventiva que inclua inspeções regulares e calibrações programadas. Isso ajudará a identificar problemas antes que se tornem sérios e a garantir que os transmissores permaneçam precisos e confiáveis.
9. Não Considerar a Interferência de Outros Equipamentos
Em ambientes industriais, a interferência de outros equipamentos pode afetar as medições dos transmissores. Ignorar essa possibilidade pode levar a resultados imprecisos. Para evitar esse erro, considere a localização dos transmissores e a presença de outros equipamentos que possam causar interferência. Se necessário, utilize blindagens ou filtros para minimizar os efeitos da interferência.
10. Não Utilizar Equipamentos Adequados
Por fim, outro erro comum é não utilizar o tipo correto de transmissor para a aplicação específica. Cada transmissor tem características e especificações que o tornam mais adequado para determinadas medições. Para evitar esse erro, avalie cuidadosamente as necessidades da sua aplicação e escolha o transmissor apropriado. Por exemplo, se você precisa medir vazão, um indicador totalizador de vazão pode ser a melhor opção.
Em resumo, evitar erros comuns na calibração de transmissores é fundamental para garantir a precisão e a confiabilidade dos dados. Ao seguir as melhores práticas e estar ciente dos erros potenciais, você pode melhorar significativamente a eficácia do processo de calibração e contribuir para a eficiência e segurança da sua operação. A calibração adequada não apenas assegura a conformidade com as normas, mas também protege a integridade dos processos industriais e a qualidade dos produtos finais.
Manutenção e Verificação Regular de Transmissores Calibrados
A manutenção e verificação regular de transmissores calibrados são práticas essenciais para garantir a precisão e a confiabilidade dos dados em ambientes industriais. Os transmissores desempenham um papel crucial na medição de variáveis como pressão, temperatura, nível e vazão, e qualquer falha em seu funcionamento pode resultar em consequências significativas, como perda de eficiência, aumento de custos e riscos à segurança. Neste artigo, abordaremos a importância da manutenção regular, as melhores práticas e as etapas necessárias para garantir que seus transmissores permaneçam calibrados e operacionais.
1. Importância da Manutenção Regular
A manutenção regular dos transmissores é fundamental para assegurar que eles operem dentro das especificações do fabricante. Com o tempo, fatores como desgaste, corrosão e variações ambientais podem afetar o desempenho dos dispositivos. A falta de manutenção pode levar a leituras imprecisas, que podem comprometer a qualidade do produto e a segurança do processo. Além disso, a manutenção preventiva ajuda a identificar problemas antes que se tornem críticos, reduzindo o tempo de inatividade e os custos de reparo.
2. Estabelecendo um Programa de Manutenção
Para garantir a eficácia da manutenção, é essencial estabelecer um programa de manutenção regular. Esse programa deve incluir a frequência das inspeções, os procedimentos a serem seguidos e a documentação necessária. A frequência das manutenções pode variar dependendo do tipo de transmissor, das condições de operação e das recomendações do fabricante. Em geral, recomenda-se realizar inspeções trimestrais ou semestrais, mas em ambientes mais exigentes, pode ser necessário aumentar essa frequência.
3. Inspeções Visuais
As inspeções visuais são uma parte importante da manutenção regular. Durante essas inspeções, os técnicos devem verificar se há sinais de desgaste, corrosão ou danos físicos nos transmissores. Além disso, é importante verificar as conexões elétricas e as mangueiras para garantir que não haja vazamentos ou desconexões. Qualquer anomalia identificada deve ser documentada e corrigida imediatamente para evitar problemas futuros.
4. Testes de Funcionamento
Após as inspeções visuais, é fundamental realizar testes de funcionamento nos transmissores. Isso envolve a aplicação de condições conhecidas (como pressão ou temperatura) e a verificação das leituras do transmissor. Os resultados devem ser comparados com os padrões de referência para garantir que o transmissor esteja operando corretamente. Se as leituras estiverem fora das especificações, pode ser necessário recalibrar o dispositivo.
5. Calibração Regular
A calibração regular é uma parte crítica da manutenção de transmissores. Mesmo que um transmissor tenha sido calibrado recentemente, fatores como vibrações, mudanças de temperatura e umidade podem afetar sua precisão ao longo do tempo. Portanto, é importante seguir um cronograma de calibração baseado nas recomendações do fabricante e nas necessidades específicas da operação. Para garantir a precisão da calibração, considere utilizar laboratórios acreditados inmetro rbc, que oferecem serviços de calibração confiáveis e de alta qualidade.
6. Documentação e Registro
A documentação é uma parte essencial do processo de manutenção e verificação. Todos os resultados das inspeções, testes e calibrações devem ser registrados de forma detalhada. Isso não apenas ajuda a manter a rastreabilidade, mas também fornece informações valiosas para futuras manutenções e auditorias. Além disso, a documentação adequada é fundamental para garantir a conformidade com as normas e regulamentos aplicáveis.
7. Treinamento da Equipe
Um programa de manutenção eficaz também deve incluir o treinamento da equipe responsável pela manutenção dos transmissores. Os técnicos devem estar familiarizados com os procedimentos de manutenção, as especificações dos equipamentos e as melhores práticas de calibração. Investir em treinamento regular ajuda a garantir que a equipe esteja atualizada sobre as novas tecnologias e métodos, melhorando a eficácia da manutenção.
8. Análise de Dados e Tendências
Além das inspeções e calibrações regulares, é importante analisar os dados coletados ao longo do tempo. Isso pode ajudar a identificar tendências e padrões que podem indicar problemas potenciais. Por exemplo, se um transmissor apresenta leituras inconsistentes em um determinado período, isso pode ser um sinal de que ele precisa de manutenção ou substituição. A análise de dados pode ser uma ferramenta poderosa para otimizar a manutenção e melhorar a eficiência operacional.
9. Manutenção Preditiva
Com o avanço da tecnologia, muitas empresas estão adotando abordagens de manutenção preditiva, que utilizam dados em tempo real para prever falhas antes que ocorram. Isso pode incluir o uso de sensores e software de monitoramento que analisam o desempenho dos transmissores e alertam a equipe sobre a necessidade de manutenção. A manutenção preditiva pode ajudar a reduzir custos e aumentar a eficiência, garantindo que os transmissores estejam sempre operacionais.
10. Conclusão
A manutenção e verificação regular de transmissores calibrados são práticas essenciais para garantir a precisão e a confiabilidade dos dados em ambientes industriais. Ao estabelecer um programa de manutenção eficaz, realizar inspeções visuais, testes de funcionamento e calibrações regulares, as empresas podem minimizar o risco de falhas e garantir a segurança e a eficiência de suas operações. Investir em manutenção não apenas protege os ativos, mas também contribui para a qualidade do produto e a satisfação do cliente.
Em resumo, a calibração de transmissores é uma prática essencial que não pode ser negligenciada em ambientes industriais e laboratoriais. A precisão e a confiabilidade dos dados são cruciais para a segurança e a eficiência dos processos, e a calibração regular é a chave para alcançar esses objetivos. Ao seguir um passo a passo adequado, evitar erros comuns e implementar um programa de manutenção regular, as empresas podem garantir que seus transmissores operem de maneira eficaz e dentro das especificações. Investir na calibração e na manutenção não apenas melhora a qualidade dos dados, mas também protege os ativos e contribui para a excelência operacional. Portanto, é fundamental que as organizações priorizem essas práticas para maximizar a eficiência e a segurança em suas operações.
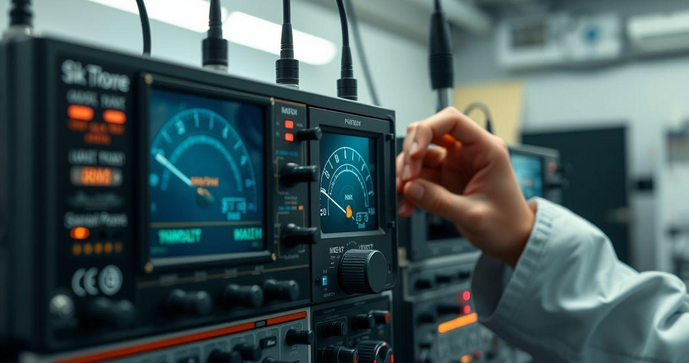
Por: Redator - 01 de Julho de 2025
A calibração de transmissores é um processo fundamental para garantir a precisão e a confiabilidade dos dados coletados em diversas aplicações industriais e laboratoriais. Com o avanço da tecnologia, a necessidade de manter os equipamentos calibrados se torna cada vez mais crítica, pois pequenas variações podem impactar significativamente os resultados. Neste artigo, abordaremos a importância da calibração, o passo a passo para realizá-la corretamente, os erros comuns a serem evitados e a importância da manutenção regular dos transmissores calibrados.
Importância da Calibração de Transmissores para a Precisão dos Dados
A calibração de transmissores é um procedimento essencial em diversos setores, incluindo indústrias químicas, petroquímicas, farmacêuticas e de alimentos. Esses dispositivos são responsáveis por medir e transmitir dados críticos, como pressão, temperatura, nível e vazão. A precisão desses dados é vital para garantir a segurança, a eficiência e a qualidade dos processos industriais. Quando os transmissores não estão calibrados corretamente, os dados que eles fornecem podem ser imprecisos, levando a decisões erradas e, consequentemente, a problemas significativos.
Um dos principais motivos pelos quais a calibração é tão importante é a necessidade de conformidade com normas e regulamentos. Muitas indústrias operam sob rigorosos padrões de qualidade e segurança, que exigem que os equipamentos de medição sejam calibrados regularmente. A falta de calibração pode resultar em não conformidade, o que pode levar a penalidades, multas e até mesmo à interrupção das operações. Além disso, a calibração adequada é frequentemente um requisito para a obtenção de um certificado de calibração rbc, que é um documento que atesta a precisão e a confiabilidade dos instrumentos de medição.
Outro aspecto importante da calibração de transmissores é a prevenção de falhas nos processos. Transmissores imprecisos podem levar a leituras erradas, que, por sua vez, podem resultar em falhas operacionais. Por exemplo, em uma planta de processamento químico, um transmissor de pressão que não está calibrado corretamente pode indicar uma pressão mais baixa do que a real, levando a uma operação insegura e potencialmente catastrófica. A calibração regular ajuda a garantir que os transmissores funcionem dentro das especificações, minimizando o risco de falhas e melhorando a segurança geral do ambiente de trabalho.
Além disso, a calibração de transmissores contribui para a eficiência operacional. Quando os dados fornecidos pelos transmissores são precisos, as decisões tomadas com base nesses dados são mais confiáveis. Isso pode resultar em uma melhor alocação de recursos, otimização de processos e redução de desperdícios. Por exemplo, em um sistema de controle de temperatura, um transmissor calibrado corretamente pode ajudar a manter a temperatura ideal, evitando o superaquecimento ou o resfriamento excessivo, o que pode resultar em perda de produto e aumento de custos.
A calibração também desempenha um papel crucial na manutenção da qualidade do produto. Em indústrias alimentícias e farmacêuticas, a precisão das medições é fundamental para garantir que os produtos atendam aos padrões de qualidade. Um transmissor que não está calibrado pode levar a variações na composição do produto, resultando em produtos fora das especificações e, potencialmente, em recalls. A calibração regular ajuda a garantir que os produtos finais sejam consistentes e de alta qualidade, protegendo a reputação da empresa e a segurança do consumidor.
Além disso, a calibração de transmissores é uma prática que pode ajudar a prolongar a vida útil dos equipamentos. Quando os transmissores são calibrados regularmente, é possível identificar problemas antes que se tornem sérios. Isso permite que as empresas realizem manutenções preventivas, evitando falhas inesperadas e custos de reparo elevados. A manutenção regular, aliada à calibração, pode resultar em uma operação mais suave e eficiente, reduzindo o tempo de inatividade e aumentando a produtividade.
Por fim, a calibração de transmissores é uma prática que promove a confiança nas medições. Em um ambiente industrial, onde decisões críticas são tomadas com base em dados, a confiança na precisão das medições é fundamental. A calibração regular ajuda a construir essa confiança, garantindo que os dados sejam consistentes e confiáveis ao longo do tempo. Isso não apenas melhora a eficiência operacional, mas também fortalece a reputação da empresa no mercado.
Em resumo, a calibração de transmissores é um aspecto vital para garantir a precisão dos dados em ambientes industriais. Ela não apenas assegura a conformidade com normas e regulamentos, mas também previne falhas operacionais, melhora a eficiência, mantém a qualidade do produto e prolonga a vida útil dos equipamentos. Portanto, investir em um programa de calibração regular é uma decisão inteligente que pode trazer benefícios significativos para qualquer organização.
Passo a Passo para Realizar a Calibração de Transmissores
A calibração de transmissores é um processo crítico que garante a precisão e a confiabilidade dos dados coletados em diversas aplicações industriais. Realizar a calibração de forma adequada requer um conjunto de etapas bem definidas. A seguir, apresentamos um guia passo a passo para realizar a calibração de transmissores, assegurando que você obtenha resultados precisos e confiáveis.
1. Preparação e Planejamento
Antes de iniciar o processo de calibração, é fundamental realizar um planejamento adequado. Isso inclui a definição do tipo de transmissor a ser calibrado, a coleta de informações sobre as especificações do fabricante e a verificação dos equipamentos necessários para a calibração. Além disso, é importante garantir que você tenha acesso a um ambiente controlado, onde as condições de temperatura e pressão sejam estáveis, pois isso pode afetar os resultados da calibração.
2. Reunir os Equipamentos Necessários
Para realizar a calibração, você precisará de alguns equipamentos essenciais, como:
- Um calibrador de pressão ou temperatura, dependendo do tipo de transmissor que está sendo calibrado.
- Um multímetro, se o transmissor for elétrico.
- Conectores e mangueiras apropriadas para a conexão entre o transmissor e o calibrador.
- Documentação do fabricante, que pode incluir gráficos de calibração e especificações técnicas.
Certifique-se de que todos os equipamentos estejam em boas condições de funcionamento e calibrados, pois isso garantirá a precisão dos resultados.
3. Desconectar o Transmissor
Antes de iniciar a calibração, é necessário desconectar o transmissor do sistema em que está instalado. Isso pode envolver a despressurização do sistema e a remoção de conexões elétricas. É importante seguir as diretrizes de segurança ao realizar essa etapa, garantindo que não haja riscos de vazamentos ou acidentes.
4. Conectar o Transmissor ao Calibrador
Após desconectar o transmissor, conecte-o ao calibrador de pressão ou temperatura. Certifique-se de que as conexões estejam firmes e seguras para evitar vazamentos. Se o transmissor for elétrico, conecte os fios de acordo com as instruções do fabricante. Verifique se o calibrador está configurado corretamente para o tipo de medição que você está realizando.
5. Realizar a Calibração
Com o transmissor conectado ao calibrador, inicie o processo de calibração. Isso geralmente envolve a aplicação de uma série de pressões ou temperaturas conhecidas ao transmissor e a comparação das leituras do transmissor com as do calibrador. Registre as leituras em diferentes pontos de calibração, que devem abranger toda a faixa de operação do transmissor.
Durante este processo, é importante ajustar o transmissor conforme necessário. Isso pode incluir a utilização de botões de ajuste ou software de configuração, dependendo do modelo do transmissor. Siga as instruções do fabricante para garantir que os ajustes sejam feitos corretamente.
6. Documentar os Resultados
Após concluir a calibração, documente todos os resultados obtidos. Isso deve incluir as leituras do transmissor e do calibrador em cada ponto de calibração, bem como quaisquer ajustes realizados. A documentação é essencial para garantir a rastreabilidade e a conformidade com as normas de qualidade. Além disso, ela pode ser útil para futuras calibrações e manutenções.
7. Desconectar e Reinstalar o Transmissor
Depois de documentar os resultados, desconecte o transmissor do calibrador e reinstale-o no sistema. Certifique-se de que todas as conexões estejam firmes e seguras. Se necessário, realize a pressurização do sistema novamente, seguindo as diretrizes de segurança.
8. Testar o Sistema
Após a reinstalação do transmissor, é importante realizar um teste do sistema para garantir que tudo esteja funcionando corretamente. Verifique se as leituras do transmissor estão dentro das especificações e se o sistema responde adequadamente às mudanças nas condições de operação. Isso ajudará a identificar qualquer problema que possa ter surgido durante o processo de calibração.
9. Manutenção Regular
A calibração de transmissores não deve ser vista como uma tarefa única, mas sim como parte de um programa de manutenção regular. É recomendável estabelecer um cronograma de calibração baseado nas recomendações do fabricante e nas necessidades específicas da sua operação. A manutenção regular não apenas garante a precisão dos dados, mas também prolonga a vida útil dos equipamentos.
Realizar a calibração de transmissores é uma prática essencial para garantir a precisão e a confiabilidade dos dados em ambientes industriais. Ao seguir este passo a passo, você estará melhor preparado para realizar calibrações eficazes e contribuir para a eficiência e segurança da sua operação. Para mais informações sobre práticas e equipamentos de calibração, consulte especialistas em Instrumentação industrial e mantenha seus sistemas sempre em conformidade.
Erros Comuns na Calibração e Como Evitá-los
A calibração de transmissores é um processo crítico que garante a precisão e a confiabilidade dos dados em diversas aplicações industriais. No entanto, existem erros comuns que podem comprometer a eficácia desse procedimento. Identificar e evitar esses erros é fundamental para garantir que os transmissores funcionem corretamente e que os dados coletados sejam precisos. A seguir, discutiremos alguns dos erros mais frequentes na calibração e como evitá-los.
1. Falta de Planejamento Adequado
Um dos erros mais comuns na calibração de transmissores é a falta de planejamento. Muitas vezes, os profissionais iniciam o processo sem uma compreensão clara das especificações do transmissor ou dos requisitos de calibração. Isso pode levar a medições imprecisas e a ajustes inadequados. Para evitar esse erro, é essencial revisar a documentação do fabricante e estabelecer um plano de calibração que inclua todos os passos necessários, os equipamentos a serem utilizados e as condições ambientais ideais.
2. Uso de Equipamentos Não Calibrados
Outro erro frequente é o uso de equipamentos de calibração que não estão calibrados ou que não estão em boas condições de funcionamento. Isso pode resultar em medições imprecisas e comprometer todo o processo de calibração. Para evitar esse problema, sempre verifique se os equipamentos de calibração, como manômetros e multímetros, estão calibrados e em conformidade com as normas aplicáveis. Além disso, mantenha um registro da calibração dos equipamentos para garantir a rastreabilidade.
3. Ignorar as Condições Ambientais
As condições ambientais, como temperatura e pressão, podem afetar significativamente os resultados da calibração. Ignorar esses fatores pode levar a medições imprecisas. É importante realizar a calibração em um ambiente controlado, onde as condições sejam estáveis e dentro das especificações recomendadas pelo fabricante. Se não for possível calibrar em condições ideais, registre as condições ambientais durante o processo e considere isso ao interpretar os resultados.
4. Não Realizar Testes de Verificação
Após a calibração, é fundamental realizar testes de verificação para garantir que o transmissor esteja funcionando corretamente. Muitos profissionais cometem o erro de não realizar esses testes, o que pode resultar em problemas não detectados. Para evitar isso, sempre execute testes de verificação após a calibração, comparando as leituras do transmissor com um padrão conhecido. Isso ajudará a identificar qualquer discrepância e a garantir que o transmissor esteja operando dentro das especificações.
5. Ajustes Inadequados
Durante o processo de calibração, é comum que os profissionais façam ajustes no transmissor. No entanto, ajustes inadequados ou excessivos podem comprometer a precisão do dispositivo. Para evitar esse erro, siga as instruções do fabricante ao fazer ajustes e evite realizar alterações desnecessárias. Além disso, documente todos os ajustes realizados para referência futura.
6. Falta de Documentação
A documentação é uma parte crucial do processo de calibração. Muitos profissionais falham em registrar os resultados da calibração, os ajustes feitos e as condições em que a calibração foi realizada. Isso pode dificultar a rastreabilidade e a conformidade com as normas. Para evitar esse erro, mantenha registros detalhados de cada calibração, incluindo datas, resultados, ajustes e condições ambientais. Isso não apenas ajuda na conformidade, mas também facilita futuras calibrações e manutenções.
7. Não Treinar a Equipe Adequadamente
A calibração de transmissores requer conhecimento técnico e habilidades específicas. Um erro comum é não treinar adequadamente a equipe responsável pela calibração. Isso pode levar a procedimentos inadequados e a resultados imprecisos. Para evitar esse problema, invista em treinamento regular para a equipe, garantindo que todos estejam atualizados sobre as melhores práticas e os procedimentos corretos de calibração.
8. Ignorar a Manutenção Preventiva
A manutenção preventiva é essencial para garantir que os transmissores funcionem corretamente ao longo do tempo. Ignorar a manutenção pode levar a falhas e a necessidade de calibrações mais frequentes. Para evitar esse erro, estabeleça um programa de manutenção preventiva que inclua inspeções regulares e calibrações programadas. Isso ajudará a identificar problemas antes que se tornem sérios e a garantir que os transmissores permaneçam precisos e confiáveis.
9. Não Considerar a Interferência de Outros Equipamentos
Em ambientes industriais, a interferência de outros equipamentos pode afetar as medições dos transmissores. Ignorar essa possibilidade pode levar a resultados imprecisos. Para evitar esse erro, considere a localização dos transmissores e a presença de outros equipamentos que possam causar interferência. Se necessário, utilize blindagens ou filtros para minimizar os efeitos da interferência.
10. Não Utilizar Equipamentos Adequados
Por fim, outro erro comum é não utilizar o tipo correto de transmissor para a aplicação específica. Cada transmissor tem características e especificações que o tornam mais adequado para determinadas medições. Para evitar esse erro, avalie cuidadosamente as necessidades da sua aplicação e escolha o transmissor apropriado. Por exemplo, se você precisa medir vazão, um indicador totalizador de vazão pode ser a melhor opção.
Em resumo, evitar erros comuns na calibração de transmissores é fundamental para garantir a precisão e a confiabilidade dos dados. Ao seguir as melhores práticas e estar ciente dos erros potenciais, você pode melhorar significativamente a eficácia do processo de calibração e contribuir para a eficiência e segurança da sua operação. A calibração adequada não apenas assegura a conformidade com as normas, mas também protege a integridade dos processos industriais e a qualidade dos produtos finais.
Manutenção e Verificação Regular de Transmissores Calibrados
A manutenção e verificação regular de transmissores calibrados são práticas essenciais para garantir a precisão e a confiabilidade dos dados em ambientes industriais. Os transmissores desempenham um papel crucial na medição de variáveis como pressão, temperatura, nível e vazão, e qualquer falha em seu funcionamento pode resultar em consequências significativas, como perda de eficiência, aumento de custos e riscos à segurança. Neste artigo, abordaremos a importância da manutenção regular, as melhores práticas e as etapas necessárias para garantir que seus transmissores permaneçam calibrados e operacionais.
1. Importância da Manutenção Regular
A manutenção regular dos transmissores é fundamental para assegurar que eles operem dentro das especificações do fabricante. Com o tempo, fatores como desgaste, corrosão e variações ambientais podem afetar o desempenho dos dispositivos. A falta de manutenção pode levar a leituras imprecisas, que podem comprometer a qualidade do produto e a segurança do processo. Além disso, a manutenção preventiva ajuda a identificar problemas antes que se tornem críticos, reduzindo o tempo de inatividade e os custos de reparo.
2. Estabelecendo um Programa de Manutenção
Para garantir a eficácia da manutenção, é essencial estabelecer um programa de manutenção regular. Esse programa deve incluir a frequência das inspeções, os procedimentos a serem seguidos e a documentação necessária. A frequência das manutenções pode variar dependendo do tipo de transmissor, das condições de operação e das recomendações do fabricante. Em geral, recomenda-se realizar inspeções trimestrais ou semestrais, mas em ambientes mais exigentes, pode ser necessário aumentar essa frequência.
3. Inspeções Visuais
As inspeções visuais são uma parte importante da manutenção regular. Durante essas inspeções, os técnicos devem verificar se há sinais de desgaste, corrosão ou danos físicos nos transmissores. Além disso, é importante verificar as conexões elétricas e as mangueiras para garantir que não haja vazamentos ou desconexões. Qualquer anomalia identificada deve ser documentada e corrigida imediatamente para evitar problemas futuros.
4. Testes de Funcionamento
Após as inspeções visuais, é fundamental realizar testes de funcionamento nos transmissores. Isso envolve a aplicação de condições conhecidas (como pressão ou temperatura) e a verificação das leituras do transmissor. Os resultados devem ser comparados com os padrões de referência para garantir que o transmissor esteja operando corretamente. Se as leituras estiverem fora das especificações, pode ser necessário recalibrar o dispositivo.
5. Calibração Regular
A calibração regular é uma parte crítica da manutenção de transmissores. Mesmo que um transmissor tenha sido calibrado recentemente, fatores como vibrações, mudanças de temperatura e umidade podem afetar sua precisão ao longo do tempo. Portanto, é importante seguir um cronograma de calibração baseado nas recomendações do fabricante e nas necessidades específicas da operação. Para garantir a precisão da calibração, considere utilizar laboratórios acreditados inmetro rbc, que oferecem serviços de calibração confiáveis e de alta qualidade.
6. Documentação e Registro
A documentação é uma parte essencial do processo de manutenção e verificação. Todos os resultados das inspeções, testes e calibrações devem ser registrados de forma detalhada. Isso não apenas ajuda a manter a rastreabilidade, mas também fornece informações valiosas para futuras manutenções e auditorias. Além disso, a documentação adequada é fundamental para garantir a conformidade com as normas e regulamentos aplicáveis.
7. Treinamento da Equipe
Um programa de manutenção eficaz também deve incluir o treinamento da equipe responsável pela manutenção dos transmissores. Os técnicos devem estar familiarizados com os procedimentos de manutenção, as especificações dos equipamentos e as melhores práticas de calibração. Investir em treinamento regular ajuda a garantir que a equipe esteja atualizada sobre as novas tecnologias e métodos, melhorando a eficácia da manutenção.
8. Análise de Dados e Tendências
Além das inspeções e calibrações regulares, é importante analisar os dados coletados ao longo do tempo. Isso pode ajudar a identificar tendências e padrões que podem indicar problemas potenciais. Por exemplo, se um transmissor apresenta leituras inconsistentes em um determinado período, isso pode ser um sinal de que ele precisa de manutenção ou substituição. A análise de dados pode ser uma ferramenta poderosa para otimizar a manutenção e melhorar a eficiência operacional.
9. Manutenção Preditiva
Com o avanço da tecnologia, muitas empresas estão adotando abordagens de manutenção preditiva, que utilizam dados em tempo real para prever falhas antes que ocorram. Isso pode incluir o uso de sensores e software de monitoramento que analisam o desempenho dos transmissores e alertam a equipe sobre a necessidade de manutenção. A manutenção preditiva pode ajudar a reduzir custos e aumentar a eficiência, garantindo que os transmissores estejam sempre operacionais.
10. Conclusão
A manutenção e verificação regular de transmissores calibrados são práticas essenciais para garantir a precisão e a confiabilidade dos dados em ambientes industriais. Ao estabelecer um programa de manutenção eficaz, realizar inspeções visuais, testes de funcionamento e calibrações regulares, as empresas podem minimizar o risco de falhas e garantir a segurança e a eficiência de suas operações. Investir em manutenção não apenas protege os ativos, mas também contribui para a qualidade do produto e a satisfação do cliente.
Em resumo, a calibração de transmissores é uma prática essencial que não pode ser negligenciada em ambientes industriais e laboratoriais. A precisão e a confiabilidade dos dados são cruciais para a segurança e a eficiência dos processos, e a calibração regular é a chave para alcançar esses objetivos. Ao seguir um passo a passo adequado, evitar erros comuns e implementar um programa de manutenção regular, as empresas podem garantir que seus transmissores operem de maneira eficaz e dentro das especificações. Investir na calibração e na manutenção não apenas melhora a qualidade dos dados, mas também protege os ativos e contribui para a excelência operacional. Portanto, é fundamental que as organizações priorizem essas práticas para maximizar a eficiência e a segurança em suas operações.